Science as a Service Accelerates Innovation in the Lab of the Future
Challenge
A leading global pharmaceutical company needed to find new ways to help their scientists focus more time and attention on innovation and strategic drug project work.
Maintaining cell lines, performing QC assays, and doing routine chromatography were consuming a large portion of scientific time. Through a series of workshops and analyses, these medium-complexity tasks were identified as key opportunity areas where substantial time savings could be realized. Re-capturing this time to focus on patent-generating science and innovation would require an increased focus on operational efficiency and standardization of routine laboratory tasks.
Solution
After an in-depth review, Avantor Services assembled an experienced scientific team to implement and manage the Science as a Service program. Scopes of Work and Service Level Agreements were developed along with a comprehensive metrics dashboard. Communication plans were also executed to build trust with the company’s researchers. Adhering to Good Laboratory Practices (GLPs), the Avantor Services team performed small molecule purifications as a service. This included normal and reverse phase purifications required to isolate newly developed compounds for advancement within the R&D project lifecycle. As an added benefit, the team also implemented system suitability checks on all walk-up purification equipment - ensuring consistency and data integrity, regardless of the operator.
Avantor Services demonstrated its commitment to quality through the delivery of detailed performance metrics focused on quality, time, and process efficiency development. Such deliverables are critical success measures for our scientists and the scientists we support.
Result
Avantor Services delivered a time savings of 7,209 direct labor hours to the customer. Throughout the course of a year, the Avantor Services team absorbed the protocol-driven work, allowing researchers to focus more time on higher level scientific functions.
The increased focus by Avantor Services on the purification process resulted in efficiency gains of more than 20% - when compared to the prior state of the overall purification process.
Given the success of this small molecule purification program, the company has now expanded the scope of Avantor Services Science as a Service program to other medium-complexity scientific areas.
Output of Avantor Services Small Molecule Purification Team | |
---|---|
Purification Requests | 320 |
Average Time Per Purification (Hours) | 16.8 |
Tasks Completed | 1,503 |
*Current at time of publication.
"Our medicinal chemistry department has been very fortunate to pilot a program using Avantor Services. They have made a tremendous impact on our medicinal chemistry efforts, particularly by providing support with purification of intermediates and final compounds, performing instrument checks, and liaising with Lab Information Systems."
— The Company’s Director of Medicinal Chemistry
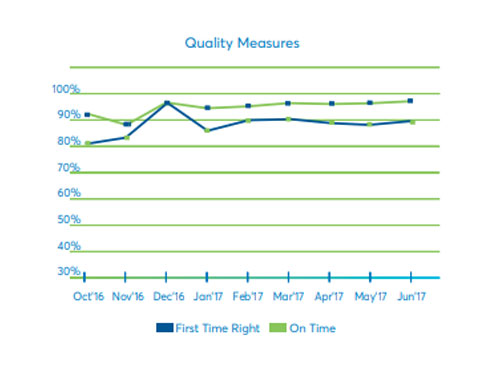
Strong commitment to quality through drivers that are critical for successful service delivery to scientists.
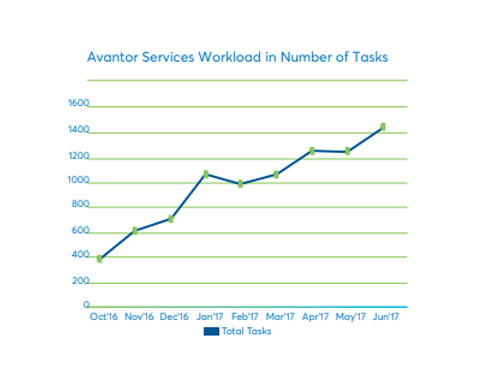
Increase in request volume proved customer confidence in Avantor Services offerings while demonstrating efficiency gains.
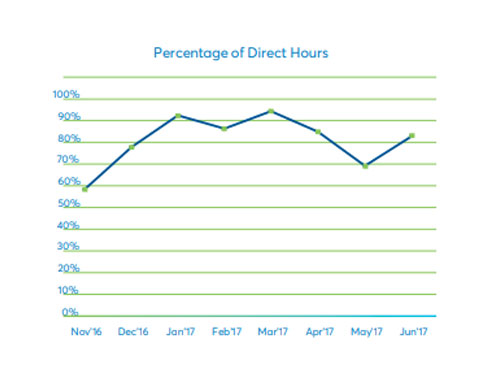
Commitment from Avantor Services to ensure our customers receive the most value for our services targeting 80% direct labor for our associates.
Learn how we developed specialized solutions and consistently delivered high-quality slides to accelerate discovery.
Learn how we helped a customer reclaim significant space, refocus 432 hours for scientists and capture $440,000 in process savings.
Learn how we helped a customer recover 16,077 hours per year for scientific research and reduced on-hand supplies by 29%.
Learn how we helped a customer realize a 36% reduction in machine downtime, 49% drop in breakages, and over 250 hours saved in direct labor per year.