SAL 10-6, >25 kGy
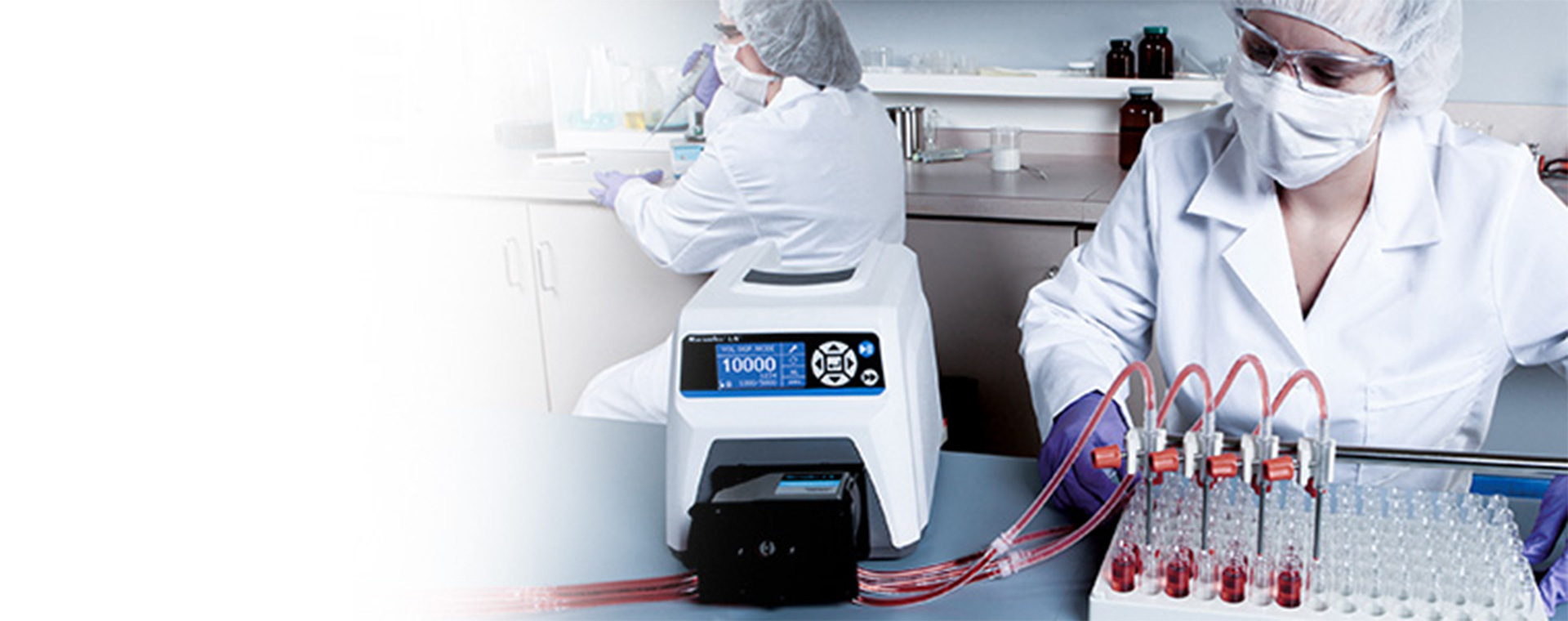
Masterflex® custom single-use bioprocess assemblies
Rely on trusted configurations that meet the highest quality in assembly and sterilization. What was once a multistep process of ordering, assembling, sterilizing, and validating now requires just one call to us. As a respected supplier of nearly every component in the bio-disposables market, we offer the widest selection of brands for truly custom fluid handling solutions.
Masterflex® single-use custom disposable sterile assemblies
- Validated brands
We custom configure, validate and package according to your specification from thousands of trusted brands. - Reduced downtime
Stop clearing and revalidating your system. We manage your inventory and send assemblies according to your schedule. - Assured quality
Our single-use assemblies are available gamma-irradiated and validated to a 10-6 sterility assurance level
Ordering your custom assemblies is easy!
Our ordering process makes it easier to get your assembly quickly and efficiently. Decrease paperwork by ordering just one custom item number. Reduce your purchasing, receiving and storage costs and eliminate wasteful downtime due to late product deliveries by letting us manage your inventory and deliver assemblies according to your schedule.
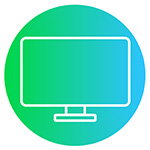
1. Map your assembly
We work with you to map the assembly and make recommendations on tubing, fitting and filter components. Our experts review and confirm each step to ensure you receive the product you need.
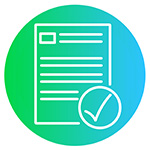
2. Quote & schematic
You will receive a quote and drawing with the details of your assembly. Upon your approval of the design, we will send a sample of the assembly for your final approval.
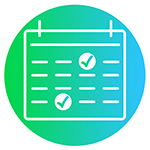
3. Delivery schedule
We work with you to establish a manufacturing and delivery schedule. We stock many fluid handing components such as tubing, fittings, filters and bags, so they are available when needed.
Examples of assembly schematics
See an example using Luer and Masterflex® Tygon tubing
See examples of Masterflex® L/S® and I/P® Y-Tubing assemblies
See an example of a Masterflex® sterile assembly filter
Sterile components
Rely on Masterflex® single-use fittings adhering to stringent sterilization protocols.
Find Masterflex® tubing ideal for the specific demands of your application.
Optimize your fluid path efficiency with Masterflex® Flow, Pressure and Temperature Sensors.
Generate precise fluid pathway flow with clamps, closures, barblocks and other Masterflex® accessories.
Masterflex single-use custom assembly FAQs
What sterility assurance level is achieved through gamma irradiation?
Why is it important to have a validated sterility assurance level?
The validated sterility assurance level (SAL) ensures that your tubing assemblies are consistently sterilized to the proper level to ensure safe operation every time. There is no need to worry that an assembly, packaging or processing variation will ruin important work or contaminate product.
Do you maintain full lot traceability?
Yes, full lot traceability is assured with every Masterflex® single-use order. Files are maintained at the production facility and Masterflex headquarters.
What type of validation documentation is provided?
A Certificate of Conformance is included with every Masterflex® single-use custom assembly order that is shipped. Additionally, a Certificate of Gamma Irradiation Processing confirming the dosage, processing date and lot number is completed for every order that is gamma irradiated. It is filed at both the production facility and Masterflex® headquarters.
What is the difference between sterile and gamma-irradiated?
The major difference between sterile assemblies and gamma-irradiated assemblies is gamma irradiated does not include testing verifying the SAL 10-6 certification. There is also a higher degree of pre-assembly component cleaning, and more details are recorded in the assembly documentation for sterile assemblies.
Both sterile and gamma-irradiated (sterilized/microbial controlled) assemblies are assembled in a cleanroom environment by gloved and gowned, trained technicians using similar packaging materials and methods. Both types of assemblies are exposed to the same amount of gamma irradiation.
Do all assemblies need to be gamma irradiated?
No, the assembly is processed and exposed to gamma irradiation based upon direction from the customer and how the assembly will be used.
What validation certifications are met at assembly locations?
Our ISO Class 7 cleanrooms (or sometimes called Class 10,000) also have the following credentials: ISO-9001, cGMP compliant.
Can customers audit Masterflex® single-use facilities?
Yes, we invite customers and prospects to visit our facilities and meet with our production and quality team. They are prepared to answer all questions and concerns.
Start your custom assembly today.
Start your custom assembly today. Our experts will help you design your custom bioprocess assembly with the brands, components and validation you need.